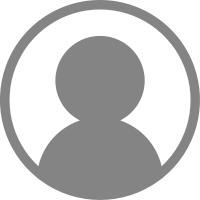
Menu
The capacity of aluminium to respond to anodising, the most familiar of finishes, makes aluminium a most important metal in a quite fundamental way. The fact that aluminium can take on this attractive, durable and tough-wearing finish makes it possible to exploit its strength and lightness in a large number of applications, particularly in building construction. Anodising essentially is an induced thickening of the natural protective oxide film on the metal's surface. It is a conversion of the parent metal and thus is not a 'coating' in the usual sense.
Unless severely deformed or stressed by excessive thermal movement, the anodic film will not chip, peel, or crack. With conventional sulphuric acid anodising, the alloys usually anodised produce a clear, hard, and extremely corrosion-resistant film capable of being coloured. The functional and decorative potential this confers on the metal is widely exploited in applications ranging from building components to domestic cookware.
Variations of the conventional electrolyte composition and process variables produce anodic coatings of distinctive functional properties. Thus, very hard anodic films are developed to provide abrasion-resistant surfaces on gears, pistons, bearings, and similar components.
Anodic films are coloured by a variety of methods. Conventional sulphuric acid films are microscopically porous, and organic or inorganic dyes and pigments may be incorporated and sealed in the film. The more durable coloured films necessary in exposed environments are more usually produced integrally with the evolution of the anodic layer and are quite permanent. Whether clear or coloured, it is important that designers understand the essential nature of anodising. Inevitably, the anodic film reproduces the physical nature of the original metal surface. Not only does this mean that any mechanical finish applied previously to the surface will be clearly evident, but even the characteristics of different metal forms will persist. Thus, an extruded element and a sheet element, if colour anodised to the same specification and placed together, will show an apparent colour difference due solely to minor but characteristic differences in surface profile peculiar to the mill process which produced them.
The basic anodising process consists of a suitable chemical pre-cleaning dip, followed by etching in a caustic soda base solution, anodising electrolytically in a sulphuric acid or other solution, and finally sealing to reduce porosity. The anodised surface is in fact an inert, and therefore a protective film of aluminium oxide. The thickness of the aluminium oxide "anodised" coating can be varied by processing time. The depth of anodised coating may be varied according to application.
• 25 Micron is recommended for heavy duty external permanent architectural applications where little deterioration can be tolerated.
• 12 Micron is suitable for internal applications, and outdoor applications where cleaning is very frequent, for example, caravan trim.
The above figures when specified are minimum figures, and film thickness is checked on a batch basis by electronic means. Colour finishes are checked for colour against standards, and tested for leaching by immersion in a boiling 0.1% borax solution.
Cleaning is desirable if the fine finish of anodised aluminium is to be preserved. Deterioration of the anodic film occurs mainly as a result of grime deposition and attack by contaminated moisture, which in a coastal environment contains chlorides and in an industrial or urban environment contains sulphur compounds. Deposited grime absorbs contaminated moisture like a sponge and holds it against the anodised surface; this permits the attack to proceed thereby damaging the film, which cannot be restored without removal. Regular cleaning is desirable, the frequency depending on accessibility and the severity of the environment. In a rural atmosphere where grime deposition and pollution of the atmosphere are at a minimum, cleaning may not be needed more frequently than every six months in order to remove deposits and restore the appearance.
In industrial and marine environments more frequent cleaning, e.g. monthly, is necessary and the maximum period between cleanings should never be more than three months. Under the worst conditions involving heavy grime deposition and atmospheric pollution by both sulphur compounds and chlorides, even more frequent cleaning is advisable if deterioration of the anodic film is to be prevented.
As a general rule, it could be assumed that with outdoor applications anodised components should be cleaned with the same frequency as windows, using the same materials and techniques.
Where an anodised surface has been neglected, it is sometimes possible to effect restoration by the use of solvents such as kerosene or mineral turpentine in conjunction with a mild household abrasive using a soft cloth. The use of harsh abrasives will damage the film beyond repair.